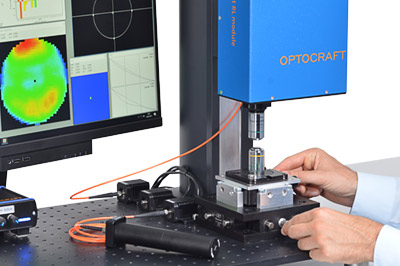
Driver-assistance systems rely on a multitude of cameras and optical sensors to increase driving comfort and safety on the road. This involves various optics which are subjected to extensive testing, not least because of the mandatory safety aspects.
Wavefront metrology is used to measure and analyse the optical quality of flat optics, such as protective windows used for LiDAR sensors. During the manufacturing process, the quality of camera lens assemblies is assessed via the transmitted wavefront. The high intrinsic stability and speed of the wavefront measurement enables the use of Optocraft’s SHSInspect modules for active adjustment and inline testing of the optical quality, as well as the monitoring of manufacturing processes. In addition to the transmitted wavefront, the Shack-Hartmann software SHSWorks determines the local slope error (beam deflection map) in µrad. A high-resolution camera can also be integrated into the measuring system to detect finer defects, e.g. scratches on the surface.Compared to classic MTF measurements, knowledge of the transmitted wavefront facilitates the identification of possible causes of errors, and provides considerably better options for comparison with simulation data. Wavefront measurement technology is also advantageous when testing flat optics such as functional protective glasses:
- adjustable wavelength
- high measuring speed
- low requirements on stability or vibration isolation
Our solution for inspecting optics for automotive applications
Systems and modules of the SHSInspect family measure the transmitted wavefront, PSF and MTF. Moreover, they provide information on colour aberrations, focal length and polarization effects and enable measurements at field points, from UV (355nm) to SWIR (1700nm).
additional Information